Обзор оборудования и технологий производства газоблока, установки.






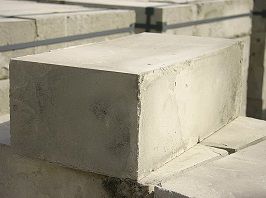
Обзор оборудования и технологий производства газоблока, установки.
В предыдущих статьях:
Производство газоблока, практически во всех случаях, сопровождается применением обычной технологии или баротехнологии. В данной статье я подробно остановлюсь на любой из таких технологий, заодно охватив вопрос применения оборудования для изготовления блоков.
Виды оборудования для производства
Передвижная установка. Баротехнология учитывает применение установок мобильного типа, рабочий принцип которых не затрагует применение пеногенератора. При помощи таких установок есть возможность делать пенобетонный блок с работоспособностью от 20 до 40 кубов материала в день, все зависит от модели. Хорошими качествами этого метода производства блоков можно назвать легкость эксплуатации и небольшую себестоимость итогового материала. Что относится к недостаткам, то тут, в первую очередь, стоит говорить о чрезмерном расходе пенообразователя, что поясняется отказом от пенообразователя. Вдобавок к этому, аппараты имеют невысокую продуктивность, а готовый пенобетонный блок имеет более плохую прочность, чем в другом варианте.
Традиционная установка для изготовления газоблока. Машины и станки традиционного типа дают возможность работать по обычной технологии, предусматривающей применение пеногенератора. Все оборудование устанавливается в общий комплекс, из-за чего в цеху образуется, своего рода, мини завод, производящий по этой технологичной схеме до 100 кубов материала в день. Преимуществом этой технологии считается невысокий расход пенообразователя, большая продуктивность аппаратуры, легкая встраиваемость в уже существующие производственные линии. Вдобавок к этому, процесс дает возможность добиться невысокой стоимости на конечный продукт, характеризуемый довольно большой прочностью, чем в предыдущем случае. И все же стоимость традиционного пенобетонного блока будет чуть-чуть выше, чем материала, сделанного в бароустановках.
Способы получения пенобетонов
1. Заливка материала в железные кассетные формы. Это известная производственная технология газоблока, позволяющая получить готовый блок за 10 часов автоклавного или неавтоклавного застывания. Когда материал наберет надёжность, стоит разобрать форму и достать готовый блок необходимой вам формы. Замечу, что одна форма доступна для применения 20 часов в день, после этого ей требуется отдых. За один день при помощи одной формы можно сделать 2 кубометра газоблока, при работе в две смены. Чем больше форм – тем больше продуктивность предприятия. Материал при этом в формах станет иметь точную форму, с самым большим отклонением от заданных показателей до 1 миллиметра. Самодельные формы разрешено использовать и дома, изготавливая блоки собственными руками. По такому вопросу на форумах имеется множество информации, которая касается бизнес-плана, чертежей, рецептов, элементов, специфик работы и продажи.
2. Резка массивов резательными установками. Резательное оборудование для изготовления газоблока сегодня есть фактически на каждом заводе, как минимум, его хотят приобрести многие. Технология учитывает заливку готового материала, произведенного из хорошего сырья, в большие 2-3-кубовые формы без перегородок. После того как застынет в течение 14 часов можно подать пенобетонный массив на резку пилами, благодаря которой вы получите такую форму и подобный размер блока, как вам нужно. Метод отличается большой технологичностью и работоспособностью.
3. Разливка материала по формам с дальнейшей распалубкой. После заливки материала в формы с перегородками, происходит 14-часовое застывание, из-за чего появляются готовые блоки. Дальше материал подается в установку, которая выполняет автоматическую распалубку. Блоки буквально выдавливаются на поддон, а формы получают автоматическую смазку. Метод выделяется высочайшей работоспособностью, но в результате вы получаете только один типоразмер готового материала.